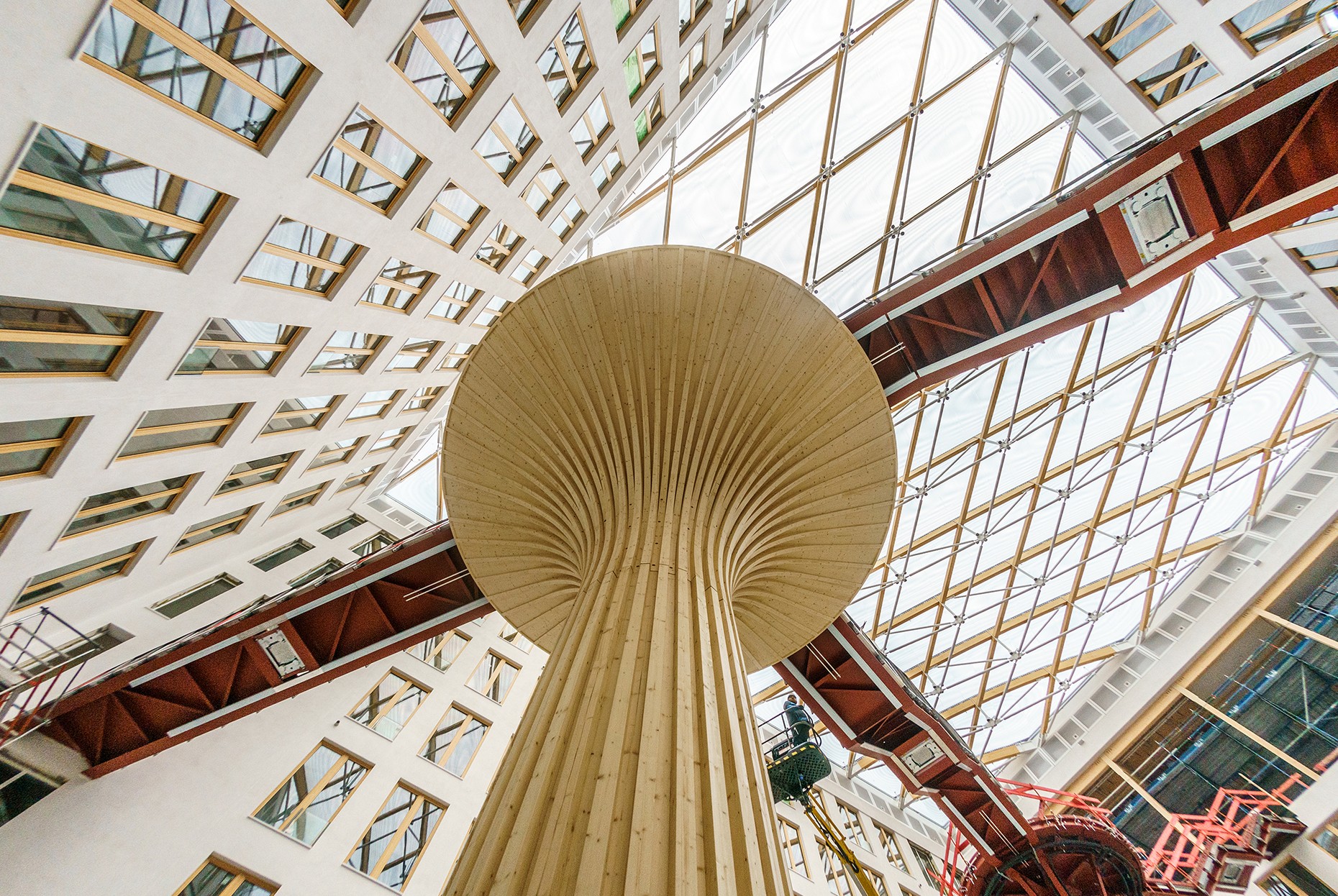
Concrete Loves Timber
Impressive timber hybrid building is sustainable flagship project
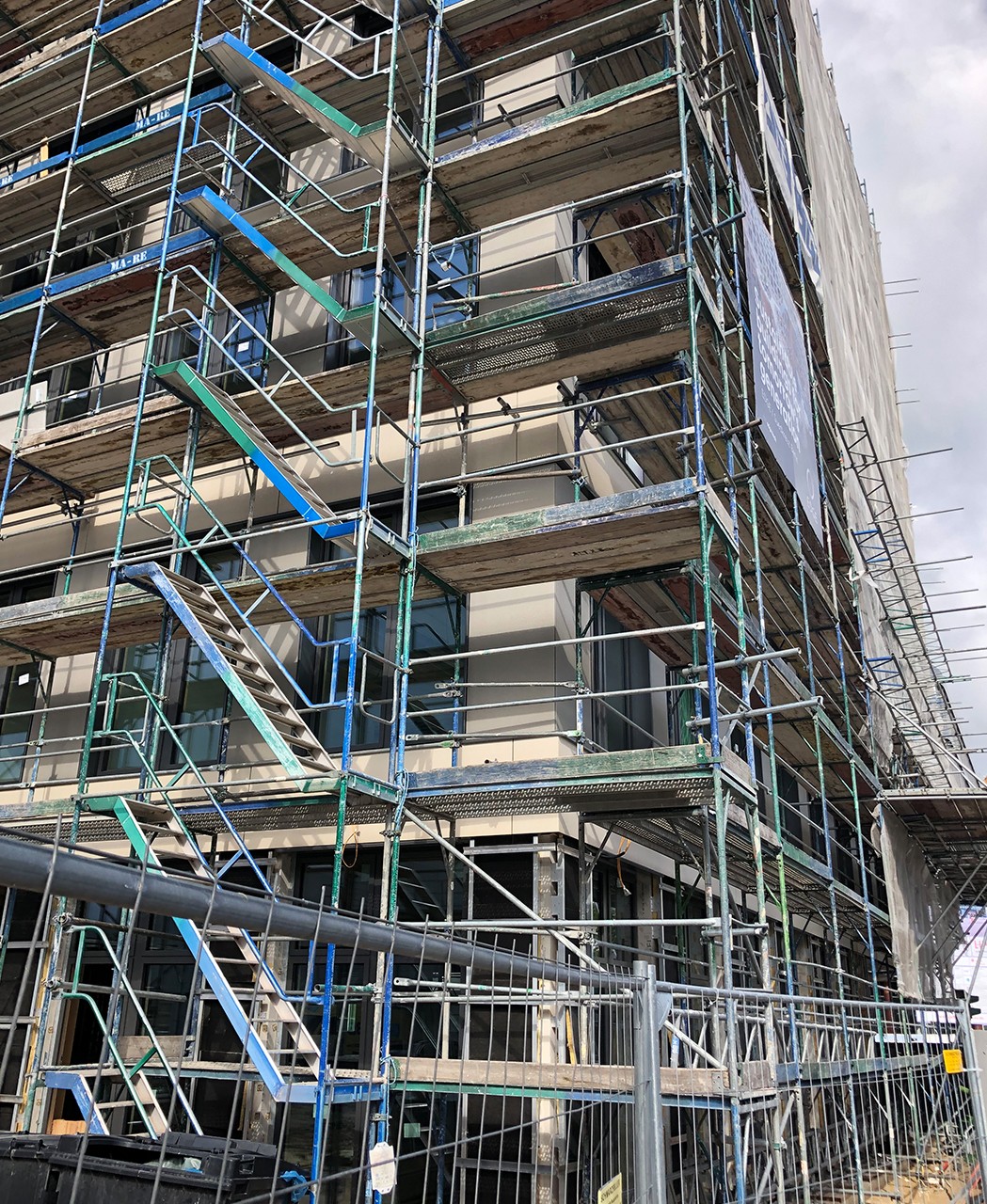
For EDGE Suedkreuz Berlin wood and concrete prove to be an unbeatable team when it comes to ecological construction. The office building planned by Tchoban Voss Architects at Schöneberger Linse with glassfibre reinforced concrete panels by Rieder is in many respects a showcase for the change that is taking place when it comes to standards for new buildings.
Concrete on wood: opposites or the new normal?
A look behind the concrete skin facade of the project reveals that a new age for real estate development is finally upon us. Germany's largest timber hybrid building shows how the needs of sustainable construction can be combined with many other requirements of a building with 32,000 square meters of floor space.
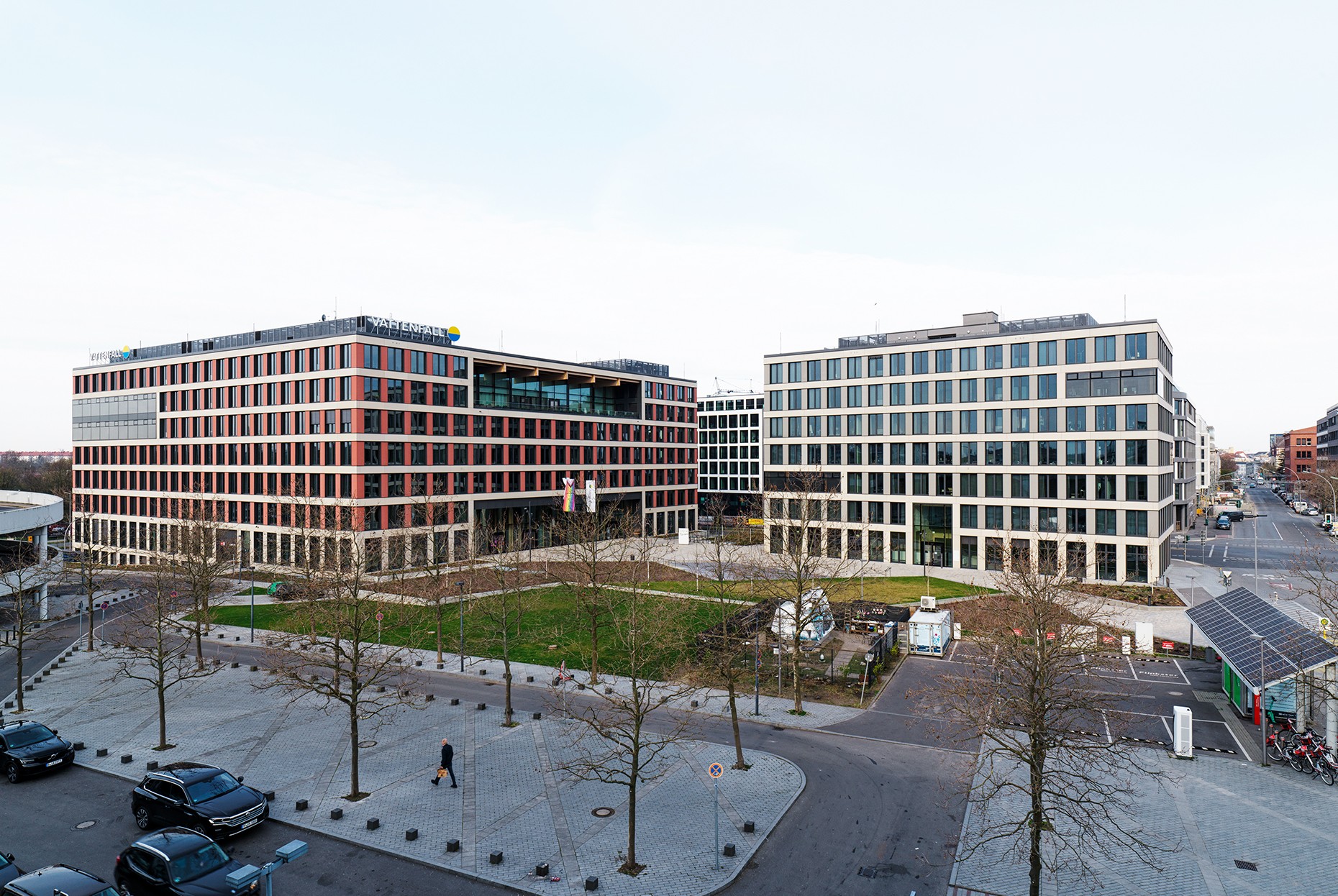
Resource-efficient, time-saving and sustainable for both people and the environment
You cannot see the exciting inner life of this visionary building at first glance. Above ground, the building extends over seven floors. Hundreds of wall elements (including windows) and over a thousand ceiling elements were manufactured in wood-concrete construction. Wall and ceiling modules were prefabricated at the factory. They were delivered to the construction site as required, where they simply had to be joined together. This saves plenty of time and storage space on site.
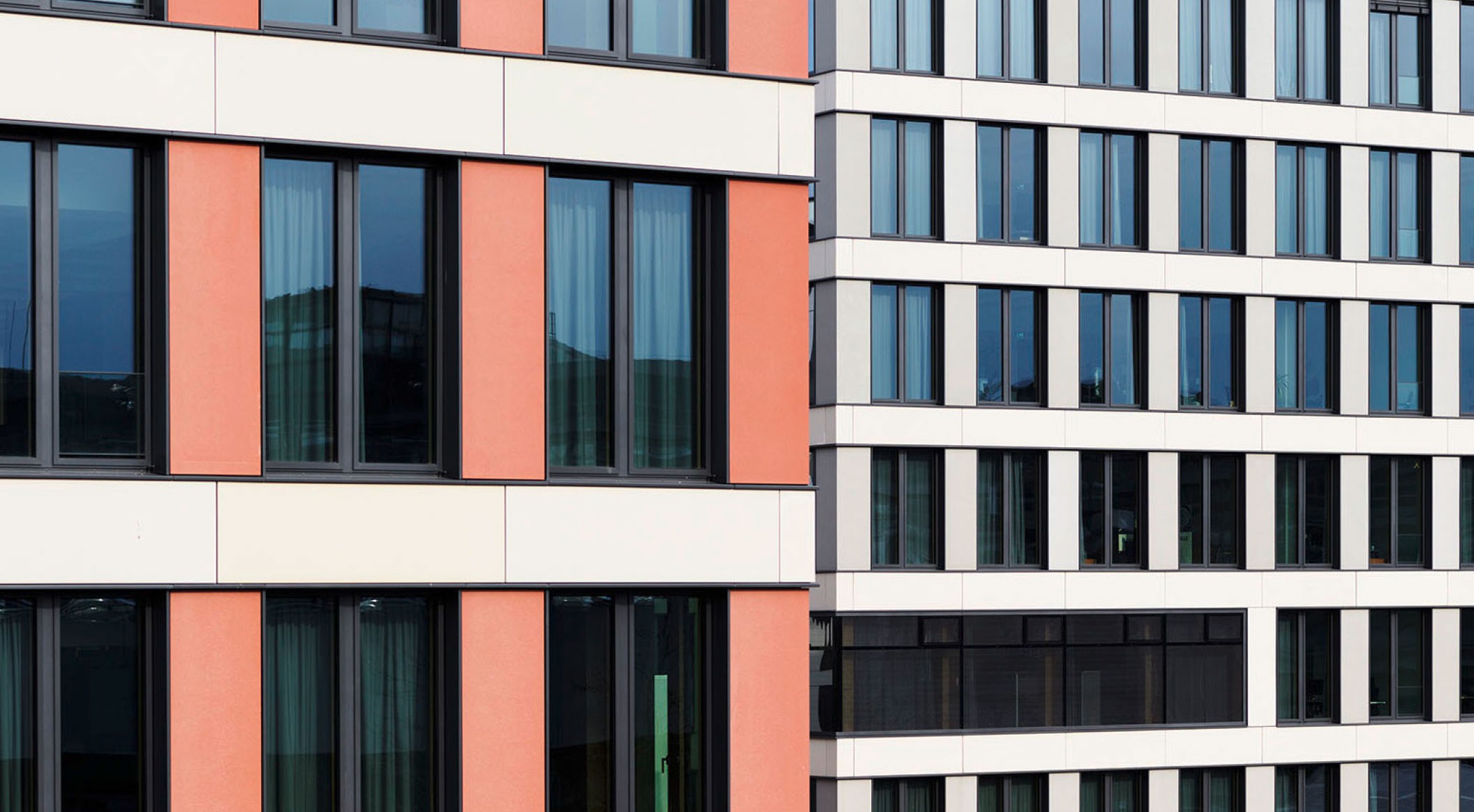
Advanced level of prefrabrication
The comparatively low weight of the facade panels was a particular advantage: "Not everything can be attached to the wall elements of the wood hybrid system: natural stone, for example, would be far too heavy. It would weigh almost 100 kilos per square meter. One element from Rieder is three times lighter!", explains architect Sergei Tchoban. In addition to the standard size of the glassfibre reinforced concrete panels, project-specific sizes can be produced easily. Pre-assembly in the factory, independent of weather conditions, guarantees a high quality standard, an efficient and flexible construction process, and rapid assembly on site. The prefabricated modules are simply hooked in on site and tweaked into place.
An exemplary case of modular hybrid residential building construction
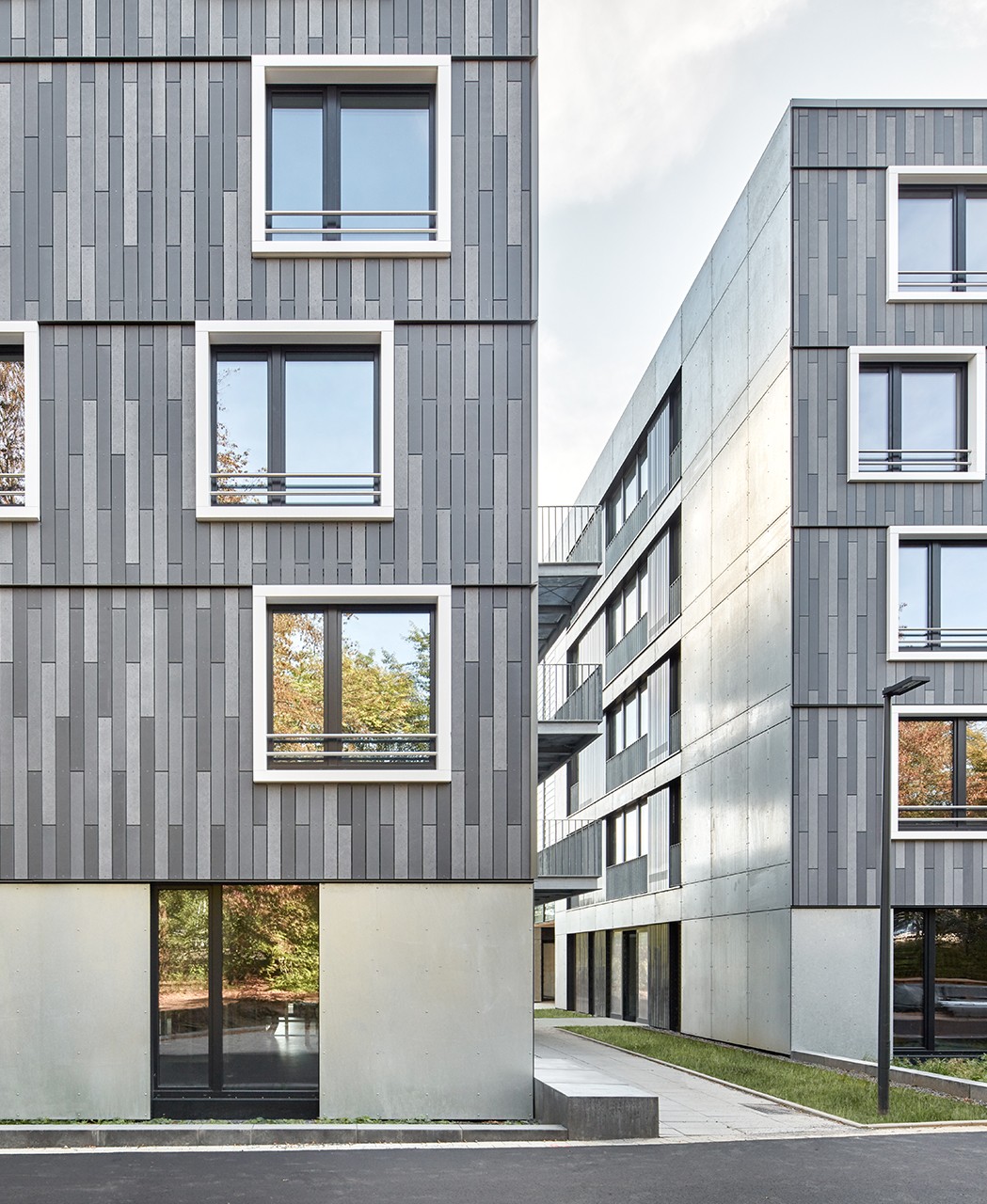
ACMS Architects designed a new building in a modular hybrid construction with 258 living spaces for students in passive house standard. The focus was on reducing construction costs and time, provide affordable housing as well as variable subsequent utilization. It was possible to reduce construction time by 10 months with a prefabricated shell, a prefabricated facade and prefabricated bathrooms.
Prefabrication
The complex was developed as a modular system consisting of prefabricated elements. The factory assembly of windows, building services and the facade resulted in ecologically optimized components with a wide range of design options.
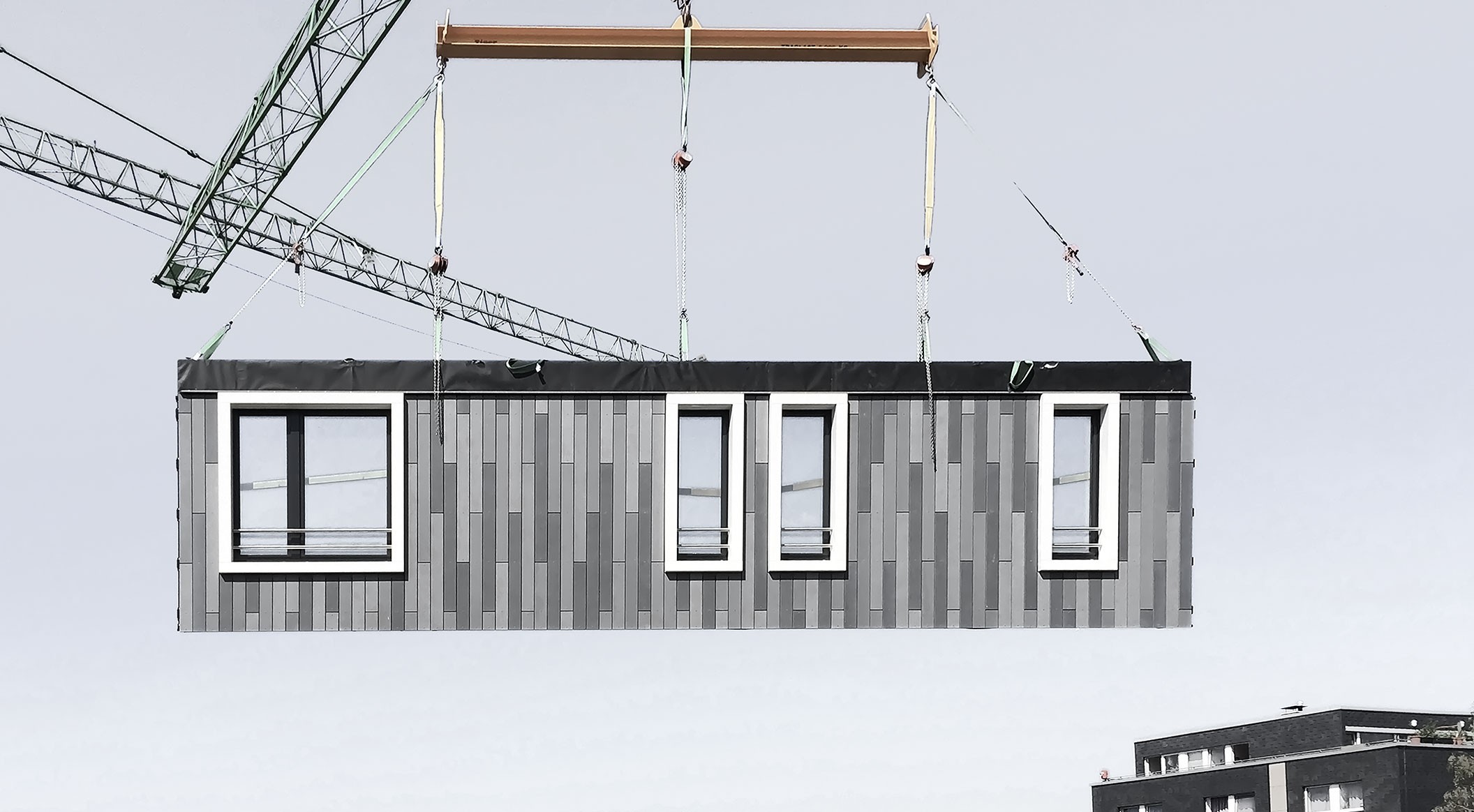
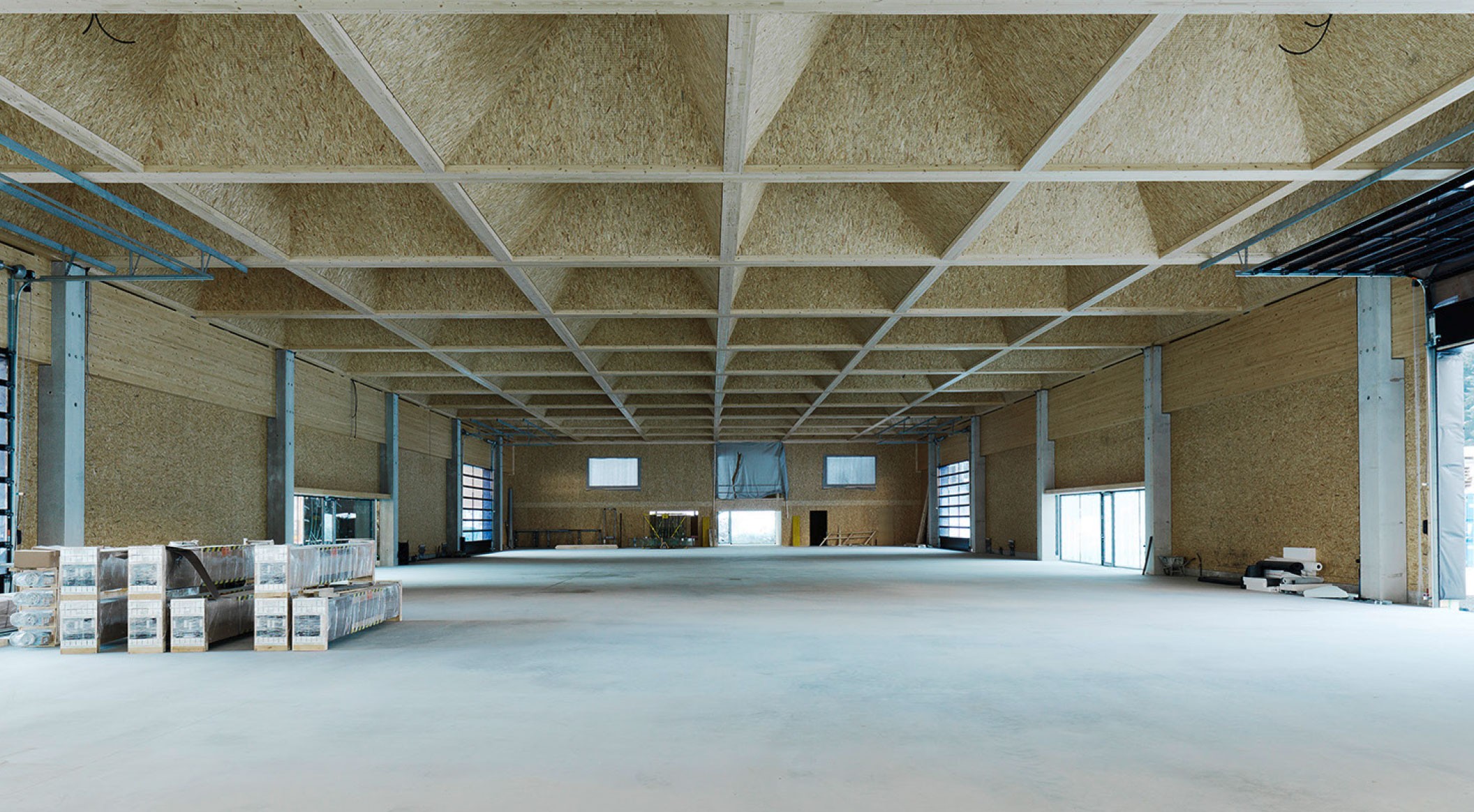